A Phoenix from the Ashes
The Fall and Rise of The Greenfields Wastewater Treatment Plant
The Greenfields Wastewater Treatment Plant (WWTP) faced an immense challenge in the summer of 2020. Days away from embarking on a construction project for improvements, a fire engulfed the plant. The Dutchess County Water & Wastewater Authority (the Authority) quickly worked with Tighe & Bond to implement an emergency response plan to prevent an environmental and human health crisis, and then regrouped on how to move forward with creating a plan to redevelop this critical component of the town’s infrastructure.
The WWTP is a small plant in the Town of Hyde Park, New York and serves the customers of the Greenfields Sewer District through 170 service connections. The plant is a tertiary treatment facility providing secondary treatment through rotating biological contactors (RBC), and tertiary treatment through gravity sand filters. The treatment plant’s original permitted average flow was 132,000 gallons per day (gpd) but was experiencing much higher flows during precipitation events.
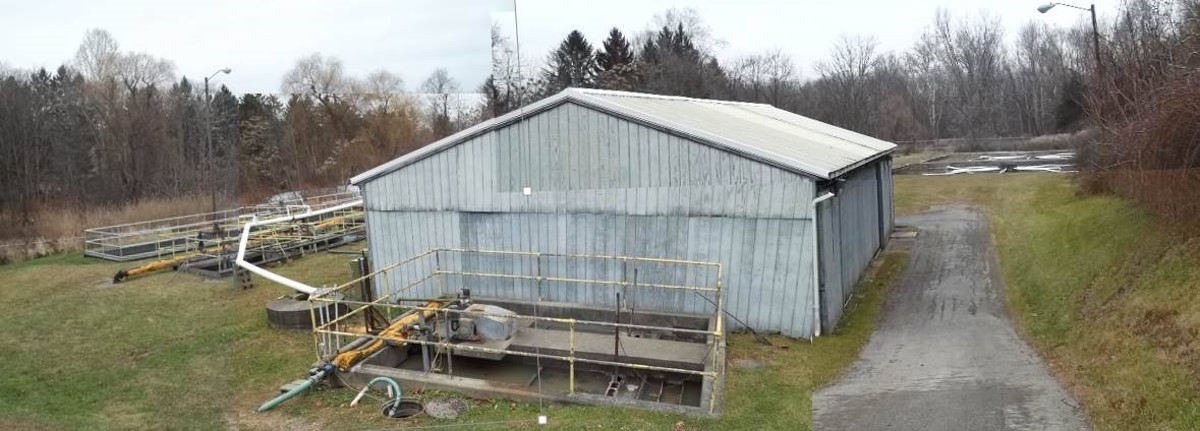
The facility housing the plant’s RBC’s before the fire.
The Original Proactive Rehabilitation Plan
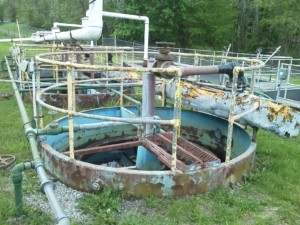
A look at the pipe corrosion within the sewer system.
To keep pace with maintenance, the Authority brought in experts from Tighe & Bond to evaluate the WWTP in 2014. The Authority’s mission is to address fragmentation and inefficiency in water and wastewater infrastructure throughout Dutchess County. The assessment uncovered that the plant was generally operating in permit compliance, but many of its components had reached or were exceeding their intended useful life. Tighe & Bond’s team also conducted a comprehensive evaluation of the collection system. Much of the system was comprised of asbestos concrete pipe installed from 1950 to 1970. The preliminary evaluation identified significant amounts of inflow within the sewer system, and sections contained sags or dips and structural deficiencies such as cracked and broken pipes.
Using the results of the analysis, the Authority worked with Tighe & Bond to complete a design for the rehabilitation of the WWTP including the installation or replacement of a bypass influent channel, inflow flow metering, primary clarifier mechanisms, RBCs, secondary clarifiers, sand filter dosing, and UV disinfection. The collection system rehabilitation plan would also reduce peak flows at the treatment plant.
The final design was completed in 2017 and construction was set to take place in 2020, but a turn of events abruptly changed the trajectory of the project for the Town, the Authority, and for the project team.
Shifting Priorities: A Swift Emergency Response
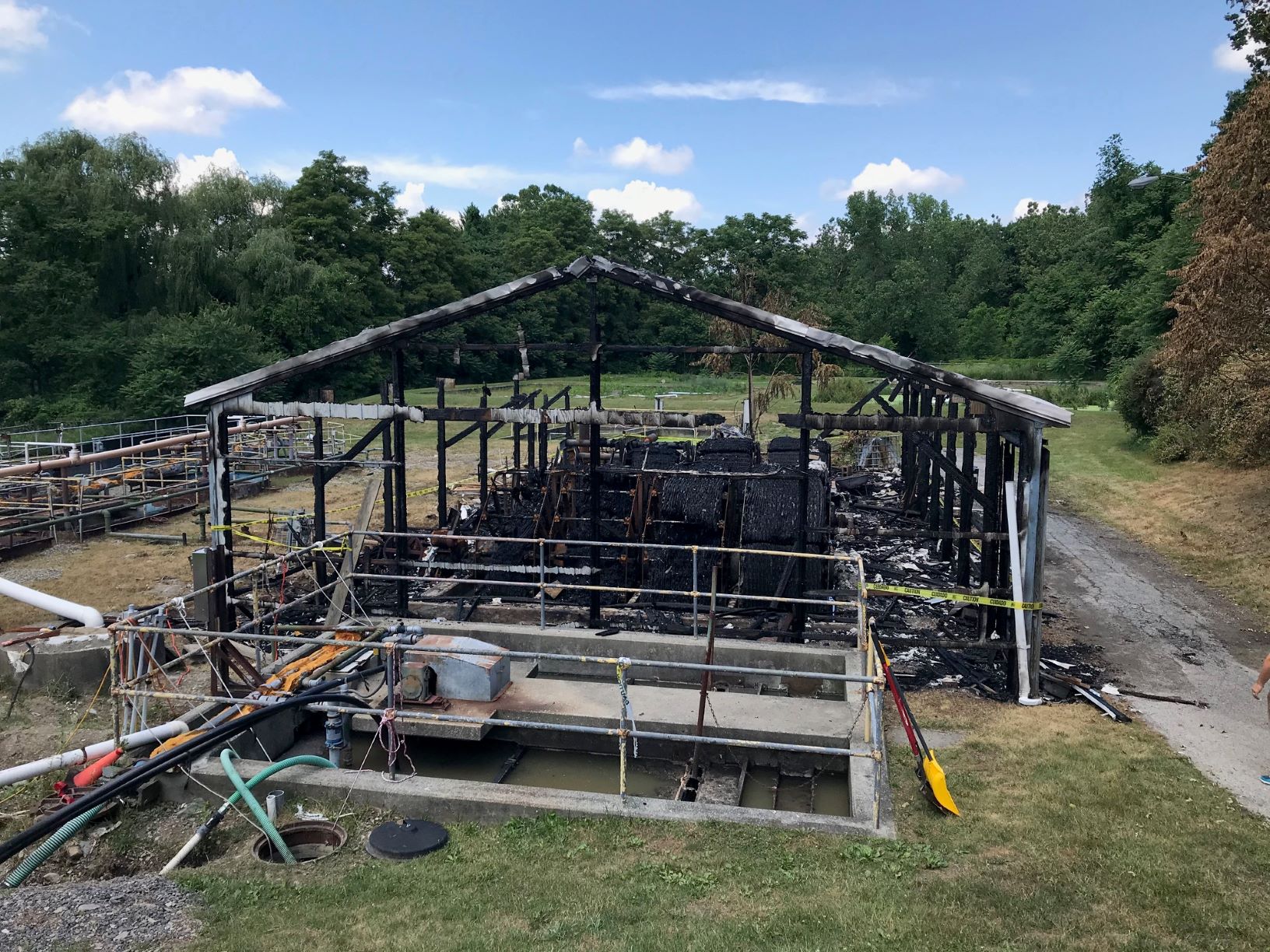
The destruction left in the wake of the fire.
Just days away from the contractor mobilization in June 2020, a fire at the plant destroyed the RBC secondary treatment system, aeration system, and chemical disinfection system. While the primary and secondary clarifiers were left unscathed, their airlift sludge removal systems were gone.
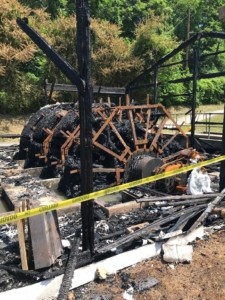
A closeup of the RBC secondary treatment system after the fire.
The Authority and Tighe & Bond quickly shifted their focus from a rehabilitation plan to an emergency fire response. On the day of the fire, the project team got to work bringing in experts from across Tighe & Bond’s Water & Wastewater Business Line to formulate an immediate action plan. With the treatment plant out of commission, the main concern was a potential health crisis. To protect the community, the project team worked with the Authority to create a three-pronged approach that meant first protecting public health, then addressing environmental health, and finally using design to increase the plant’s treatment capabilities.
“Tighe & Bond often tries to explain the value of having a ’deep bench,’, but when our client needed us, no one hesitated to jump right in and contribute to the emergency response problem solving which really made a deep impact on our client’s ability to respond,” explained Senior Project Manager Erin Moore. “I have worked with the DCWWA since 2008, and highly value our relationship. Their staff deeply appreciated our efforts, and I don’t know if I was ever so proud to be part of Tighe & Bond’s wastewater team or more appreciative of our company culture.”
Executing a Multi-Phase Plan
In order to protect the health of the community connected to the Greenfields WWTP, wastewater disinfection needed to be restored immediately. With guidance from the project team, the Authority called on neighboring facilities to contribute the dosing pumps and sodium hypochlorite supplies to restore the wastewater disinfection in a matter of hours.
The second step was the restoration of post-aeration. Oxygen in the treated wastewater effluent is critical to the health of aquatic species in the receiving water. Tighe & Bond sized the blower needed for post aeration and quickly located a local supplier to provide a replacement. The electrical contractor on the project also pitched in setting up temporary power for the blower by extending power access all the way to the far end of the site and procuring necessary variable frequency drives (VFDs) allowing post aeration to be restored 28 days after the fire.
The final stage of the emergency response was the restoration of the plant’s treatment capabilities. While many options were considered, the approach that allowed for rapid deployment was enhanced coagulation (a form of chemical wastewater treatment that allows for solids to separate from the water and be filtered out more quickly). Tighe & Bond reached out to a coagulant vendor representative who visited the site the day after the fire to test different coagulants using jar testing. A coagulant type and dose were selected from the testing results.
An important consideration was determining at what point in the treatment process to dose the coagulant. A varied approach to dosing at the RBC effluent and secondary clarifier influent was necessary to work in tandem with progressing construction activities. With no indoor facility, the team knew they would have to keep the coagulant from freezing during the approaching fall and winter. They planned for the plant to use many layers of coverings and portable heaters. Carrier water was used to ensure the velocity of the water was high enough to also prevent freezing and that it would reach the plant’s clarifiers. Enhanced coagulation was in full operation just 21 days after the fire.
“Upon learning of the catastrophic facility fire that destroyed components of our wastewater treatment plant, Tighe & Bond immediately gathered their resources, devised a strategy, and collaboratively worked with our team through the venture. We felt reassured having them by our side throughout the process, from temporary measures to restore normal operations,” says Dutchess County Water & Wastewater Project Facilitator Jonathon Churins.
Designing a Brighter Future
- Completed replacement Secondary Clarifiers with the new dosing pumps in the background.
- The new RBC units under individual FRP covers.
After taking the first steps to protect people’s health, the environment, and provide treatment, the focus accelerated to providing the successful approval, delivery, installation, and startup of new RBC units. Working amidst the COVID-19 pandemic and industry-wide manufacturing delays, the new RBC units arrived on site and were placed in service in February and March 2021. After an 8-week startup and commissioning process, the new RBC units were fully operational and providing secondary treatment of BOD and ammonia.
Other elements of the WWTP design were in progress amidst the immediate priority of the RBC units to provide the plant to not just meet operation requirements but ensure a safe, efficient, and effective treatment system for the community. These elements included a new influent channel and flow meter, primary clarifiers, secondary clarifiers, sand filter dosing pumps and controls, UV disinfection, post aeration, sludge blowers, and a sludge pumping system.
The new secondary clarifiers were a complete replacement of the old clarifiers, upgrading the circular metal tanks to a rectangular concrete tank matching the style of the existing primary clarifier tank and providing new clarification mechanicals. A new pumped sludge removal system replaced the antiquated airlift removal system that was destroyed in the fire. The new sludge pump station serves both the primary and secondary clarifiers. The sand filter dosing pumps replaced the existing aged pumps with new, more efficient units and an improved control system that automated pump and sand filter cycling.
UV disinfection replaced the existing chlorine dosing system. Half of the chlorine contact tank was converted into the UV channel, with the other half remaining as a contact chamber along with the chlorine dosing point to allow for emergency chlorination. The post-aeration tank was provided with dedicated, redundant blowers to provide air to the diffusers. The sludge holding tanks were supplied with a single dedicated blower for mixing the stored solids.
At the head of the WWTP, a bypass chamber and second influent channel were added to allow flexibility in operation and to handle high flow events. A new influent flow meter was constructed after the headworks.
As of November 2021, the WWTP was fully operational with all temporary systems decommissioned and the new secondary treatment, disinfection, and post-aeration equipment in use. This project continues to serve as a successful example of coordination and immediate response to a devastating emergency to address the health of the community and environment followed by a strategically planned shift to vital plant improvements.
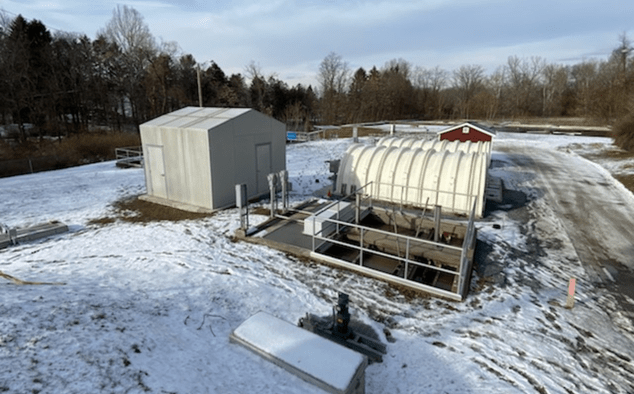
Completed WWTP as seen from the Operations Building. Visible are the sludge pump station, primary clarifiers, and RBC units.